Experimenting with Lasercutting and Etching
- Charlotte biszewski
- Dec 13, 2018
- 2 min read
Updated: Aug 11, 2021
I was invited to take part in a print exchange. Something which I haven’t done for years, and I was keen to use it to further my experimentation. The print is based on a binary clock (yes I don’t know what it is either) based at a hospital, local to me in Bristol.
I began using my Cricut machine, which is a tabletop cutter, about the size of a regular printer. I wanted to cut out some of the circles from the binary clock – something which is difficult to achieve with hand drawing, I wanted to explore how I could combine this CAD process with a very traditional form of craft.
This was from a plate I found in the scraps at Spike Print Studio, submerging it directly as an open bite into a saline solution – I liked the texture it produced. I also like the immediacy of the shapes. In one picture you can see how I have recut into the work with the laser engraver. I am, however completely baffled at how this has happened, this texture and how it has etched this way.
If only it was this simple… When it came to repeating this processes at the studio in the Wroclaw Academy I was not so lucky. As imagined the solution bit right into the etching plate, without giving it a grain or texture. I have since written to the technician at Spike and their solution is the same recipe as it is here. So I was baffled. Now I could have put an aquatint on and been done there, but I was in the mood to experiment and I remember the assistant telling me that you can spraypaint a car paint onto the zinc and then etch this away with the lasercutter. He admitted they had done little research into this, so I felt like it might be worth trying.
Here are some of the plates I made which sampled different textures, time in solution and dot sizes. I think the final thing to try is to look at is how to get the finest lines – with raster and vector comparisons. For next time.
These were cut on the Trotec laser cutter. The bottom two images were using a greyscale rather than a bitmap, so they are lacking shading. I found the cutter needed to go over the images twice and then it was best to wash under water – avoid wiping as this gave scratches and uneven detail. In the bath – some foul biting was occurring after about 5 or 6 minutes. I don’t mind about this, but it might be worth trying out other makes of metal spray to find the best cover. Or you could try spraying more, but I don’t know how this would affect the laser engraving.
This was the final plate.
I think if you look in the picture on the right, you may notice it has bitten unevenly. I think I did not degrease properly. But otherwise, the bite was good. The textures were made up in photoshop, from different mezzotint (hah!) and noise settings. On the whole, I am pretty happy with the result and feel I am on the edge of an exciting process.
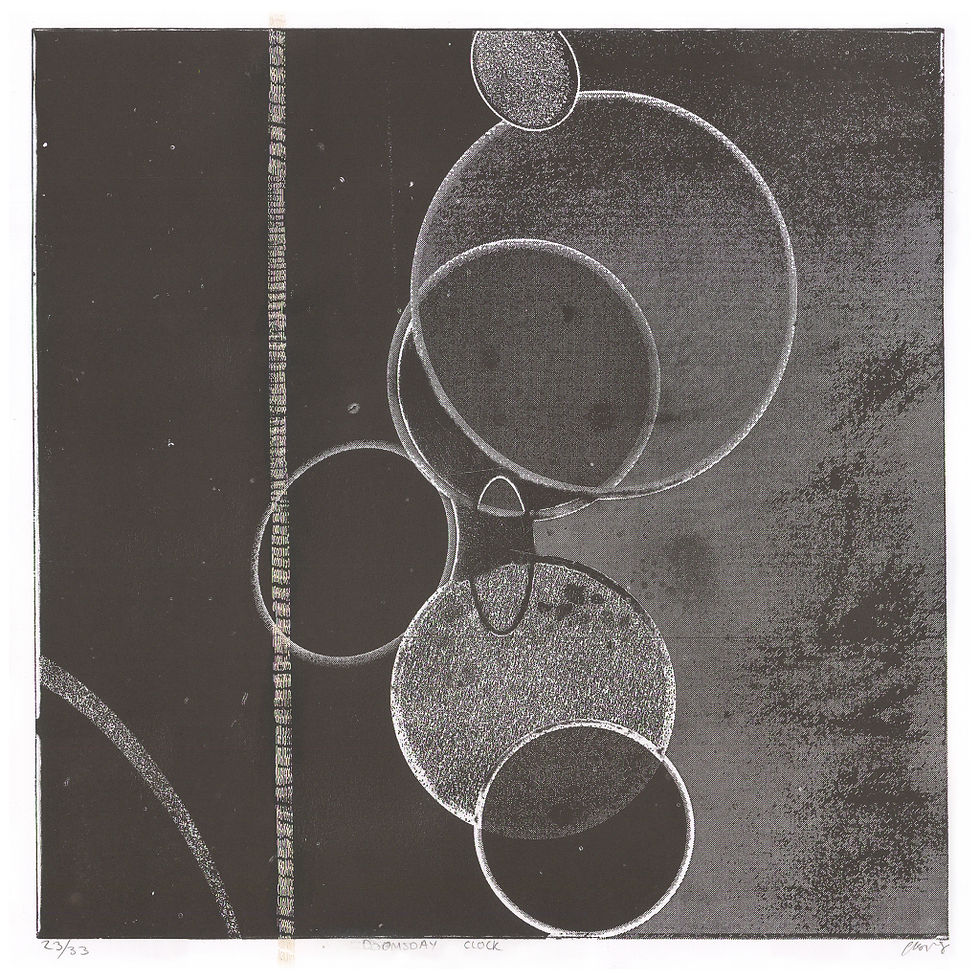
Comments